知見・論考
デジタル実験によるメカ設計のための定量モデルの作り方
設計理論式DX
本稿では、メカ設計上流における定量モデル(設計対象の本質を捉えた数式を中心に客観的・論理的にしめしたもの)の新しい作成手法について概説します。本方法は現実の実験を重ねて定量モデルを得る従来の方法と異なり、CAEによるデジタル実験を通して定量モデルを定式化することが特色です。本方法の採用により、人間の限界を超えた設計空間の探索が可能となります。これにより、エキスパート設計者でも対応が困難であった設計課題に対して新しい解決策を導くことも可能になります。
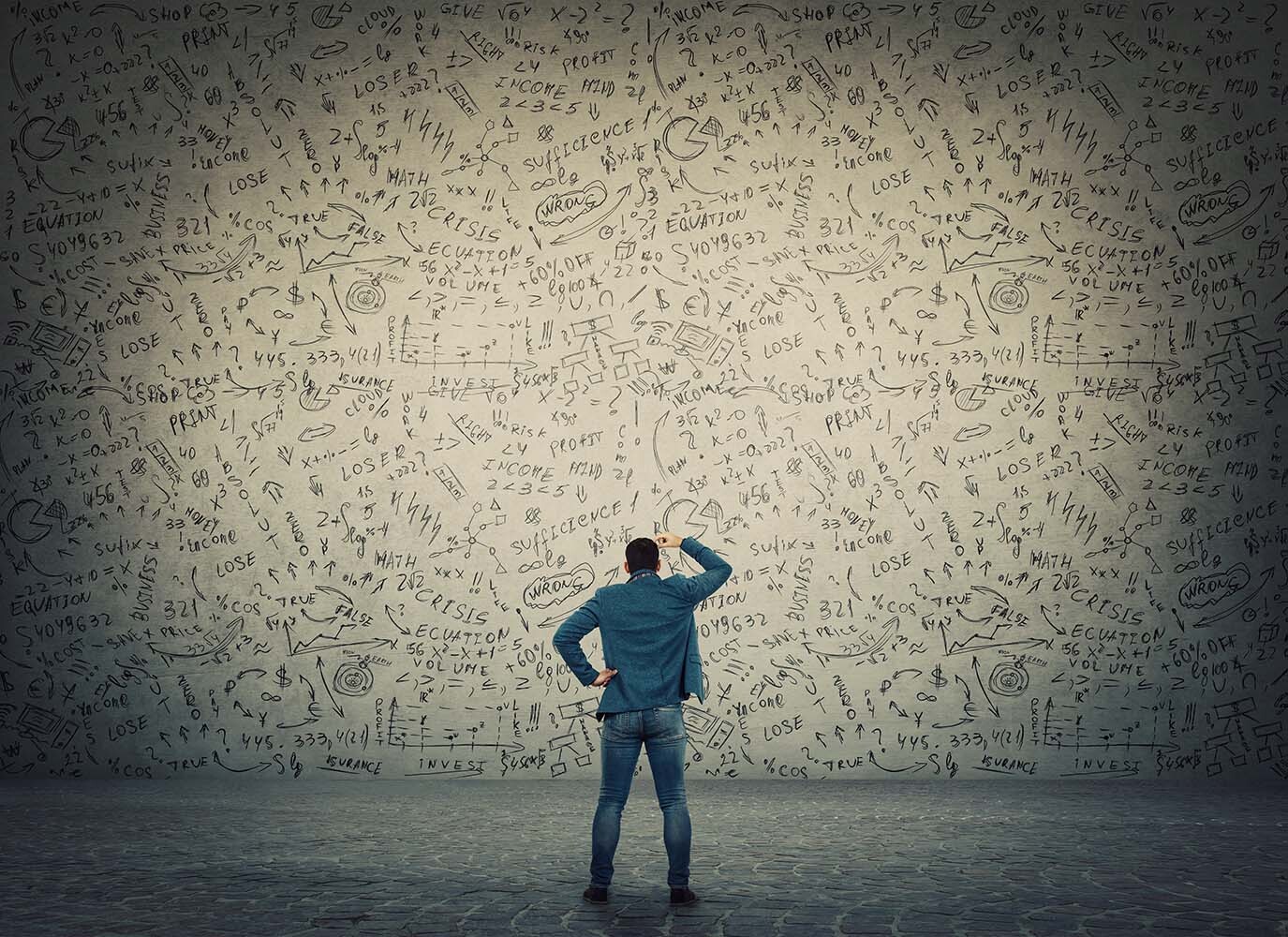
メカ設計の「人間臭さ」
CAE/CAD導入により設計の効率化は進んでいるものの、メカ設計現場には未だに「人間臭さ」が強く残っています。特に開発上流における目標仕様や重点課題、検討手順・方法といった設計方針を、設計者が個人のスキルで決めている場合が多くあります。過去の類似製品の編集で済ましている事業領域もあります。或いは、明確な設計方針等の十分な事前検討がないまま、CAE/CADツールを走らせているケースも散見されます。
事前の明確な設計イメージを持たないことは、設計検討の対象パラメータに考慮の抜けが生じ、不備のある設計に繋がります。材料中のマイクロバブルや分子配向といったミクロな環境条件を代表として、現実世界のあらゆるパラメータを人間が考慮することは人間にとって不可能です。とは言え、材料や寸法、表面処理といった目に見える(マクロな)要素を代表として、設計者が想定・制御可能なパラメータも多くあります。ところが、設計方針がないと、制御するパラメータが過小となり品質の低い設計に留まってしまいます。これが、後に不具合流出を引き起こすことになります。
また、仮に考慮すべきパラメータを事前に全て想定できていたとしても、人間はパラメータ間の関係を過度に単純化した認識をしがちです。代表的な誤認識(バイアス)は、経験・勘・度胸(いわゆるKKD)に基づく推量です。過去の経験値から、勘に基づいて新しい設計値の候補を想像し、複数の候補から度胸で新しい設計値を選択してしまうのです。そして、経験値から新しい設計値への推量には単純な線形的な関係を想定してしまいがちです。しかし、現実にはパラメータ間の関係は非線形的であることの方が多く、経験・勘・度胸に基づいた設計が現実と大きく乖離してしまいます。
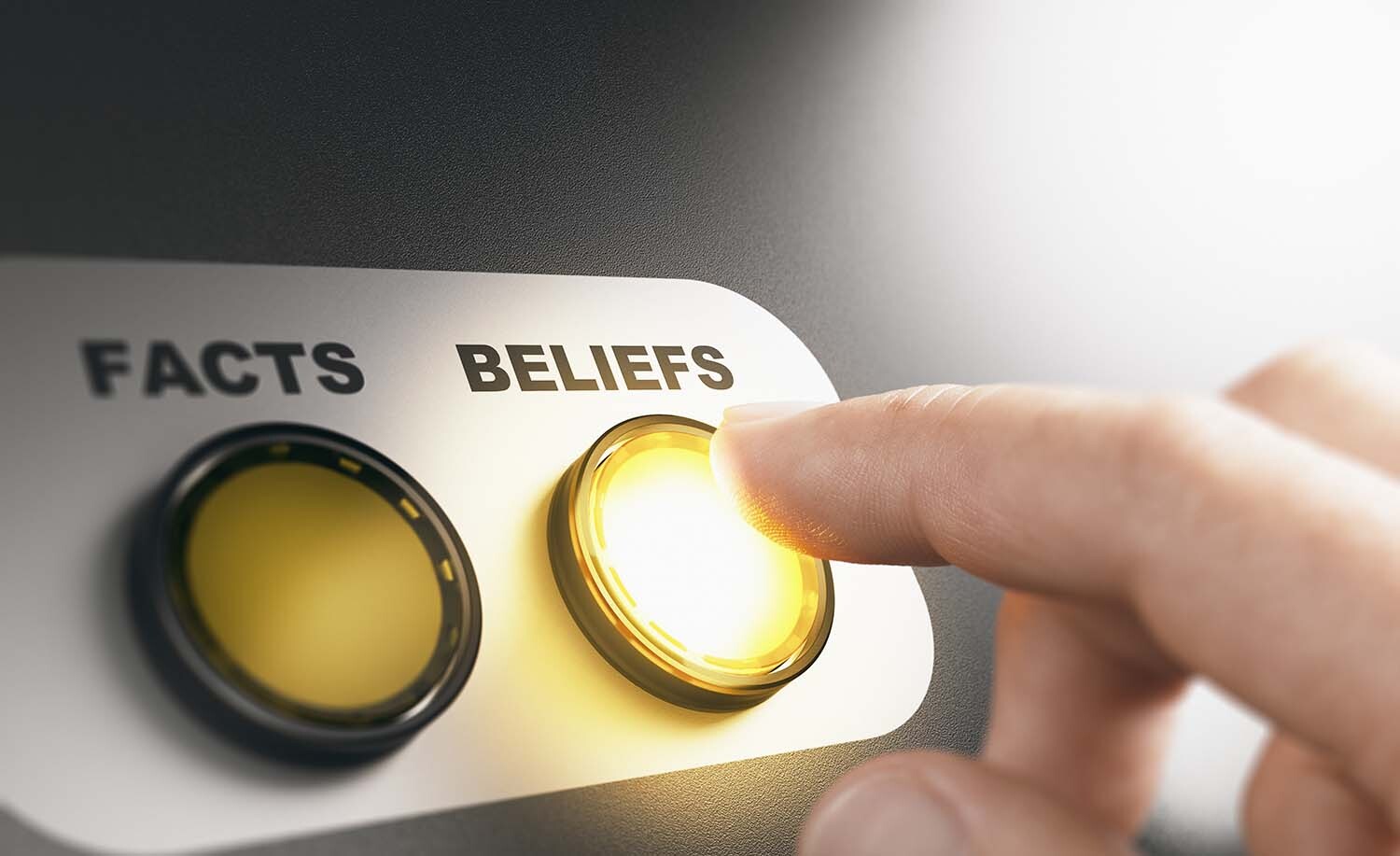
定量モデルの有効性
パラメータの考慮漏れや過度の単純化を回避するためには、メカ設計上流において定量モデルをきちんと作成し活用することが有効です。定量モデルとは、前稿 [1]で説明した通り、設計対象(製品・機能)の本質を捉えた数式を中心とし、客観的・論理的に表現したものです。定量化することにより、設計対象の製品・機能をどの設計者でも等しく明確にイメージできます。さらに、早期にモデルを作成し予測・検証をすることで、設計で考慮すべきパラメータやパラメータ間の関係に気付くことができるようになります。
デジタル実験による帰納的な定量モデル作成
定量モデルの作成方法は、演繹法と帰納法の大きく2通りです。演繹法は、物理学的な原理・法則や数学的な定理といった理論から設計に必要な数式を導く方法です。帰納法は、実験等の経験データから、パラメータ間の関係式をあぶり出す方法です。メカ設計における演繹法の例としては、梁の構造計算やねじの軸力計算などがあります。帰納法の例としては、疲労限界の推定式などがあります。
しかし、メカ設計における定量モデル作成は難しい課題でした。演繹的方法は、理想化された物理現象を表現しています。メカ設計が対象とする現実のマルチフィジックスで複雑な現象に対しては適用のハードルは高いのです。
一方、従来の帰納的方法も、膨大なリソースが必要となる実験がハードルでした。つまり、測定機材を用意し、サンプルを多数作成し、多くの時間を実験と分析に費やす必要がありました。さらに設計者の業績評価が製品設計で決まる以上、設計空間を広く探索する実験を行う動機は薄く、リソースも与えられないことがほとんどです。
そこで、当社では、デジタル実験による帰納法という、新しい定量モデル作成法を考案しました。本方法は既に当社の顧客企業との実践例があり、顧客企業が長年解決できていなかった設計課題の解消に繋げています。
新しい定量モデルの作成法手順は以下の通りです(図1);
1. 設計対象の定義
設計課題を明確化した上で、求めたい特性値(アウトプット)、インプットとする製品パラメータ(以下、インプット・パラメータ)を取捨選択します。インプット・パラメータの選択においては、①設計者がコントロール可能、②アウトプットにクリティカルに影響、③計算リソースを鑑みて現実的、であることを主な判断基準とします。たとえば、設計課題が衝撃に対する製品筐体の強度だとすると、求めたいアウトプットを剛性(等価断面2次モーメント)とします。クリティカルに影響するインプット・パラメータとして筐体の代表寸法(高さ、幅、奥行、壁厚)などとします。このステップは最初に試行錯誤が必要で、設計者が最も注力が必要なステップです。
設計課題を明確化した上で、求めたい特性値(アウトプット)、インプットとする製品パラメータ(以下、インプット・パラメータ)を取捨選択します。インプット・パラメータの選択においては、①設計者がコントロール可能、②アウトプットにクリティカルに影響、③計算リソースを鑑みて現実的、であることを主な判断基準とします。たとえば、設計課題が衝撃に対する製品筐体の強度だとすると、求めたいアウトプットを剛性(等価断面2次モーメント)とします。クリティカルに影響するインプット・パラメータとして筐体の代表寸法(高さ、幅、奥行、壁厚)などとします。このステップは最初に試行錯誤が必要で、設計者が最も注力が必要なステップです。
2. インプット・パラメータの範囲の設定
変化させるインプット・パラメータとその上下限値(すなわち設計空間内の定義域)を決めます。上下限値は所与の設計制約にとらわれずに、可能性の端択のために広めに決めます。
変化させるインプット・パラメータとその上下限値(すなわち設計空間内の定義域)を決めます。上下限値は所与の設計制約にとらわれずに、可能性の端択のために広めに決めます。
3. CAE解析条件の設定
試行的なCAE解析を通して、自動かつ連続でCAE解析を効率的に実行できる最適解析条件を探索・設定します。たとえば、自動連続CAE解析の精度を担保しながら、計算時間を極小化できるようにするために、自動メッシュなどの設定を探索し設定します。この設定値の検証を疎かにしているCAE解析の現場は意外と多いです。
試行的なCAE解析を通して、自動かつ連続でCAE解析を効率的に実行できる最適解析条件を探索・設定します。たとえば、自動連続CAE解析の精度を担保しながら、計算時間を極小化できるようにするために、自動メッシュなどの設定を探索し設定します。この設定値の検証を疎かにしているCAE解析の現場は意外と多いです。
4. 自動連続CAE解析
先に設定したインプット・パラメータの範囲とCAE解析時間をもとに、求めたいアウトプットに対して適切なアルゴリズムを用いてパラメータの組合せを生成します。その組合せに基づいて、CAEを自動で連続的に実行します。CAE内容やCAEリソースに大きく依存しますが、一例として金曜日の夕方から月曜日の朝までの間に1,500ケース実行しました。
先に設定したインプット・パラメータの範囲とCAE解析時間をもとに、求めたいアウトプットに対して適切なアルゴリズムを用いてパラメータの組合せを生成します。その組合せに基づいて、CAEを自動で連続的に実行します。CAE内容やCAEリソースに大きく依存しますが、一例として金曜日の夕方から月曜日の朝までの間に1,500ケース実行しました。
5. 定式化と検証、定量モデル化
多数の解析結果を最もよく表現する数式を決定します。たとえば、決定係数R2などを判断基準として、多項式の次数や項数、関数形(三角関数、対数関数など)などを決め、具体的な係数・定数を持つ数式を決定します。
定式化後の検証として、得られた数式の精度の評価と、適用範囲の適切な設定は非常に重要なステップです。しかしながら、設計理論式を既に活用されている設計現場でもこの検証のステップを見過ごされてしまうようです。本稿での具体的な検証方法の提示は割愛させていただきます。明文化されたアウトプット、検証済みの数式、選別されたインプット・パラメータが揃って定量モデルとなります。
多数の解析結果を最もよく表現する数式を決定します。たとえば、決定係数R2などを判断基準として、多項式の次数や項数、関数形(三角関数、対数関数など)などを決め、具体的な係数・定数を持つ数式を決定します。
定式化後の検証として、得られた数式の精度の評価と、適用範囲の適切な設定は非常に重要なステップです。しかしながら、設計理論式を既に活用されている設計現場でもこの検証のステップを見過ごされてしまうようです。本稿での具体的な検証方法の提示は割愛させていただきます。明文化されたアウトプット、検証済みの数式、選別されたインプット・パラメータが揃って定量モデルとなります。
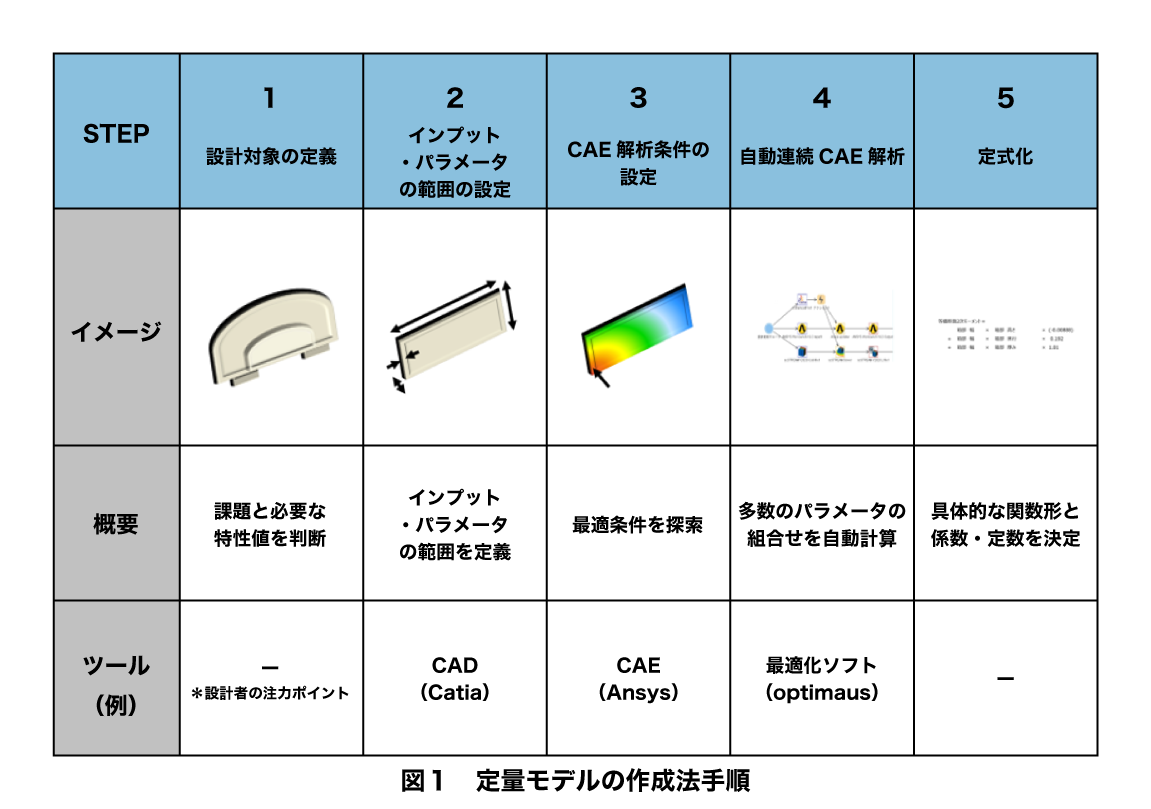
デジタル実験による帰納法には以下のメリットがあります;
• 暗黙知の形式知化が不要
従来は、エキスパート設計者が勘所として抑えていた暗黙知を形式知化するために、丹念なヒアリングをしながら定量モデルを作っていく必要がありました。本方法では暗黙知の源泉となっている設計パターンと同数かそれ以上のパターン数をCAEで行えます。そのためエキスパート設計者からのヒアリングによる暗黙知の形式知化は必須ではなくなります。
従来は、エキスパート設計者が勘所として抑えていた暗黙知を形式知化するために、丹念なヒアリングをしながら定量モデルを作っていく必要がありました。本方法では暗黙知の源泉となっている設計パターンと同数かそれ以上のパターン数をCAEで行えます。そのためエキスパート設計者からのヒアリングによる暗黙知の形式知化は必須ではなくなります。
• 現実の制約を超えた設計空間まで探索可能
将来トレンドを先取りした設計を試作しながら行うことには困難が伴います。確実性の低い試作に十分な投資を許容してくれる環境はなかなか存在しません。あるいは、試作を支えるサプライヤーがまだ存在しない場合もあります。しかし、デジタル実験であれば設計空間に限界がありません。
将来トレンドを先取りした設計を試作しながら行うことには困難が伴います。確実性の低い試作に十分な投資を許容してくれる環境はなかなか存在しません。あるいは、試作を支えるサプライヤーがまだ存在しない場合もあります。しかし、デジタル実験であれば設計空間に限界がありません。
• ニーズに寄り添った定量モデルが作成可能
本方法では事業・製品のニーズに沿い、設計者が設計現場で使える過不足のない定量モデルを作成できます。
本方法では事業・製品のニーズに沿い、設計者が設計現場で使える過不足のない定量モデルを作成できます。
• 製品構造が大きく変わった場合にも円滑に設計可能
製品構造が大きく変わり、過去に作成した定量モデルが適用出来なくなった場合にも本手法は利点を発揮します。比較的短期間に新しい定量モデルが作成可能なので、定量モデルに基づいた設計を継続することが可能です。
製品構造が大きく変わり、過去に作成した定量モデルが適用出来なくなった場合にも本手法は利点を発揮します。比較的短期間に新しい定量モデルが作成可能なので、定量モデルに基づいた設計を継続することが可能です。
ただし、デジタル実験による帰納法には以下の制約や限界もあります。
• CAEのリソースが必要
CAEのリソースとして、ソフトウェア、計算機、CAEに習熟したオペレーターが必要になります。ただし、試作にかけるリソースとの比較において、CAEのリソースの方が高コストになる場面は一般的に多くありません。また、CAEを受託するサービスも日本国内だけでも多数あり、内部にCAEリソースをもつ必要はありません。
CAEのリソースとして、ソフトウェア、計算機、CAEに習熟したオペレーターが必要になります。ただし、試作にかけるリソースとの比較において、CAEのリソースの方が高コストになる場面は一般的に多くありません。また、CAEを受託するサービスも日本国内だけでも多数あり、内部にCAEリソースをもつ必要はありません。
• 設計者には、設計対象をモデル化するためのスキルが必要
設計者はモデル化された結果を容易に受け入れることができますが、自らモデル化することに不慣れな場合が少なく、モデルを作るスキルは類似製品の編集で済ましてきた設計現場においては培われていないことがほとんどです。この点を経験豊富な当社が支援します。
設計者はモデル化された結果を容易に受け入れることができますが、自らモデル化することに不慣れな場合が少なく、モデルを作るスキルは類似製品の編集で済ましてきた設計現場においては培われていないことがほとんどです。この点を経験豊富な当社が支援します。
• 定量化/計算できないことはモデル化できない
CAEが実行できない問題の場合には、別のアプローチが必要です。たとえば、人工知能(AI)の活用が検討候補になります。
CAEが実行できない問題の場合には、別のアプローチが必要です。たとえば、人工知能(AI)の活用が検討候補になります。
これら制約や限界を超えるべく、本手法の導入にあたっては当社が設計者と伴走しながら責任をもってサポート致します。
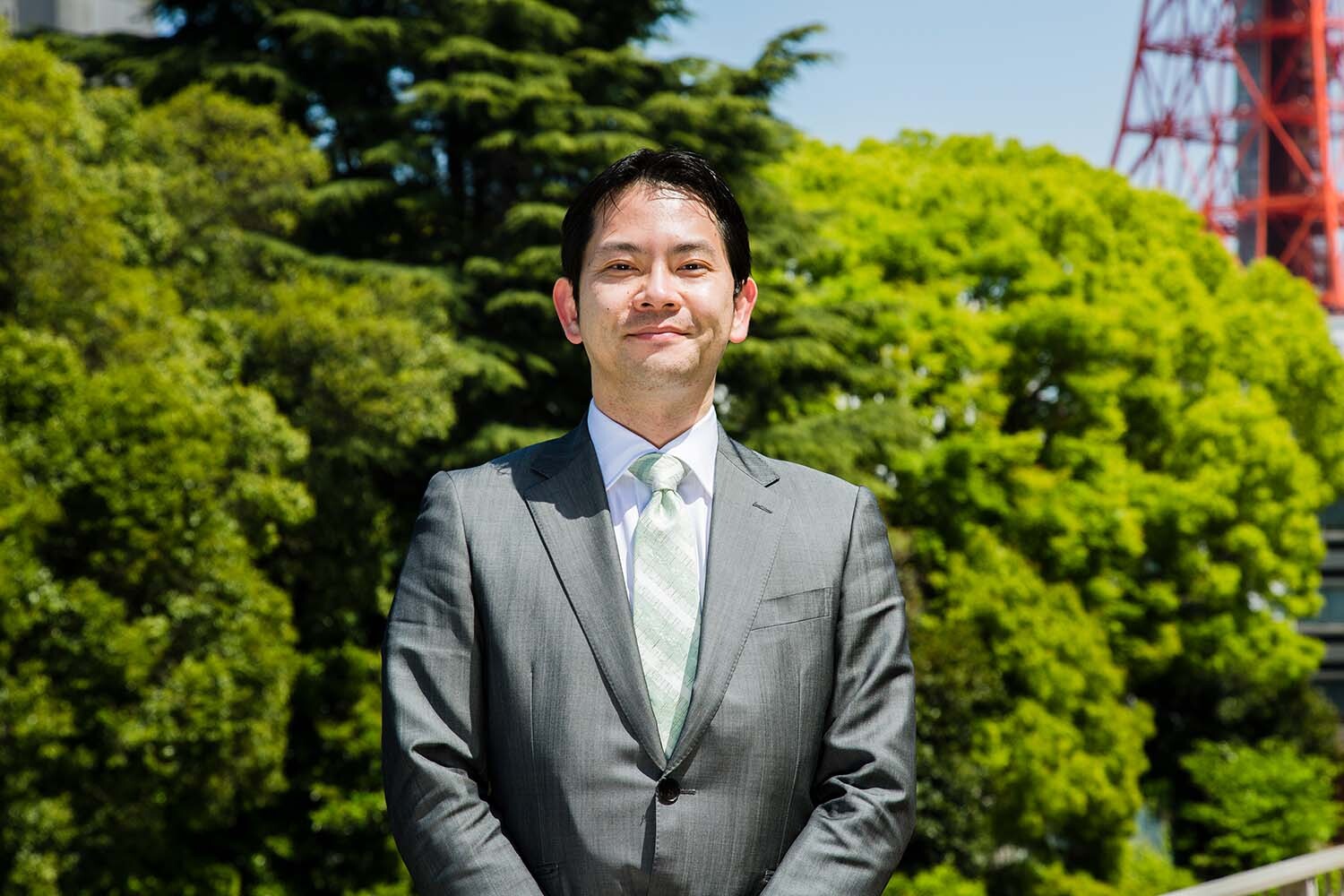
【参考文献】
[1] https://www.mediocritas.com/discussion/detail/17
[1] https://www.mediocritas.com/discussion/detail/17