知見・論考
NQが変える製品化プロセスの在り方
NQ
前記事[1]では、「NQの全点モニタリング型のアプローチは、生産段階だけでなくバリューチェーン全体に適用されます」と述べました。本記事では、NQが変える製品化プロセスの姿と、その実現のために必要な業務フロー見直しや最新テクノロジー活用について説明します。
全点モニタリング型の製品化プロセス
NQの「全点モニタリング型のアプローチ」[1]を適用した製品化プロセス(下図)では、まず企画(開発初期)段階にて「要件とトレーサビリティ(以下、トレサビ)を確立」します。その上で、設計段階にて「全パターン検証」、生産段階にて「条件モニタリング」、そして両段階にて「品質モニタリング」を行います。以下、各段階について順に説明します。
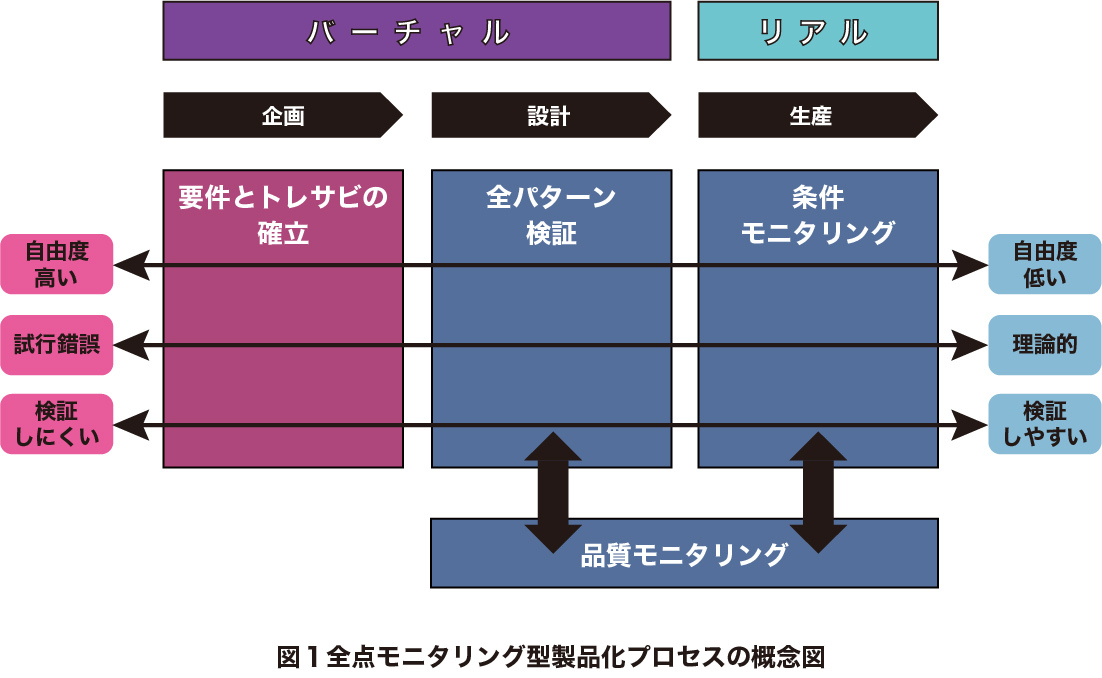
要件とトレサビの確立
全点モニタリング型の製品化プロセスの実現には、まず企画段階で要件とトレーサビリティを確立することが不可欠となります。ここに要件は、顧客要件や生産要件等、製品化に必要な全ての要件を含みます。また、トレサビは、顧客要求~要件~機能~仕様を互いに紐づけ、変更管理や課題管理のために追跡可能にすることを指します。つまり、顧客要求を要件としてヌケモレなく定義し、機能・非機能に分解・整理し、さらに各機能の仕様まで関連付けながら落とし込みます。たとえば、製品筐体等の機構設計をイメージすると、「ドアを強く閉めた衝撃でスイッチが外れない」という顧客要求を受け、「50Gで取り付け部が動かず破壊されない」といった設計要件を定義し、そのための仕様として「50Gの人力に耐えうる保持力、強度」といった具体的な仕様を明確化し、互いに関連付けて管理します。回路設計やソフト設計、工程/設備設計でも同様です。NQでは、こうした要件とトレサビの確立のために、要件の自動抽出AIやトレサビ管理ソフトの活用を検討しています。
品質モニタリング
要件とトレサビを確立しておくと、設計段階での「品質モニタリング」が可能になります。設計段階における品質モニタリングとは、全要件に紐づく設計の品熟の進捗を常時監視することです。たとえば、部品強度に関する設計では、設計がどの段階にあり、幾つの仕様が達成できたのか、未達成の仕様は目標に対してどの程度まで満足する状態に達しているのか、といった進捗状況を定量的に監視します。ソフトウェア開発であれば、全ての設計(基本設計~実装)がコンピュータ上で行えるため、こうした進捗の自動モニタリングは既に当たり前のように行われつつあります。NQでは、企画段階で要件とトレサビを確立しておき、さらに機構・回路・工程・設備等の設計もバーチャル化することにより、管理工数のかからない設計段階での品質のモニタリングを可能にします。
トレサビに基づく設計段階の品質モニタリングを行えば、審査ゲートを必要としない開発プロセスが可能になります。従来、ほとんどの企業では、製品化プロセスを製品化企画、製品化計画、詳細設計といった段階に分け、各段階の節目でデザインレビュー(DR)を行い、知見者による審査(いわば品質チェック)が行われていました。このようなやり方では、DR毎にしか品熟度がわからず、そこで本質的な問題が発覚すると後戻りが生じていました。また、デザインレビューは知見者の経験値に基づいて行われるため、審査項目のヌケモレが発生する場合も多くありました。しかし、トレサビに基づいて設計段階から品質モニタリングを行えば、設計の品熟度が常に把握できるため、課題抽出・対策実行や次のプロセスへの移行判断を都度行うことができるようになります。
また、トレサビの管理システムを活用した課題管理や設計-生産連携も効率化できます。たとえば、設計/工程の故障モード影響解析(DFMEA/PFMEA)では、企画段階で洗い出した仕様に主要な故障モードを紐付ける形で可視化し、さらに課題の刈り取りも行えば、検討漏れを防ぐことができます。また、DFMEAもPFMEAも同じトレサビ情報に紐づけるため、DFMEA-PFMEAの連携もしやすくなります。たとえば、設計上の工夫で解決できない課題を工法・工程でカバーするよう設計部門から工程部門へ課題を引き継ごうとしても、正しく管理されず忘れられてしまうという事例が多くの企業で見られます。しかし、トレサビに紐づけて管理することでそうした検討漏れを防ぎやすくなります。
全パターン検証
設計段階における「全パターン検証」では、バーチャル空間上で要件を満たす設計モデルの全パターンを検証し、最適解を導出します。製品筐体等の機構設計で言えば、従来はベテラン設計者が当りをつけた設計をし、部分的なシミュレーションや試作品を作って検証し、問題があればやり直すというやり方が普通でした。NQにおいては、考えられる構造パターンを網羅的に探索・検証し、必要な強度や耐熱性といった仕様を達成できる最適な構造を見つけ出します。
まず概念・構想設計段階では、ベテラン設計者が持っていた暗黙知を、科学的根拠に基づく数式に置き換えます。具体的には、1DCAEに代表される設計理論式や、多目的設計探索(MODE)などの手法を活用します。設計理論式は仕様を満たす設計の概略を数式で表現したものです。設計最初期から活用することで、若手設計者でも目指す設計の方向性を掴むことができます。設計理論式は、物理・科学理論や過去の設計情報に基づいて構築するため、設計者が単に勘で当りを付ける方法に比べて検討の網羅性が向上し、検討漏れやムダが解消されます。また、MODEはトレードオフになる設計要素を可視化する手法で、不具合を生じない設計仕様をすぐに特定できます。弊社では、自動車部品メーカーや機械部品メーカーにおいて設計理論式や多目的設計探索法を用いて問題解決に繋げた実績があり、具体的な手法構築・活用のノウハウを蓄積しています。
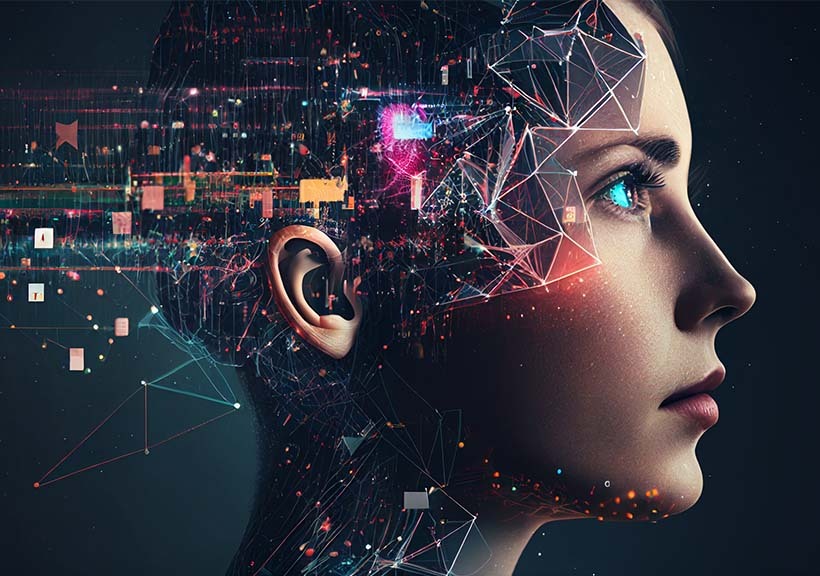
詳細設計段階では、3DCAEと組合せたマルチフィジックスでの最適化計算を行います。従来はCAEツールの機能やコンピュータの処理能力に限界があり、当りを付けた限られたパターンや、応力や熱などそれぞれの単一観点でのみシミュレーションや試作を行っていました。しかし、近年はCAE手法/ツールの発展や、スーパーコンピュータ等ハイパフォーマンスコンピューター(HPC)の普及が進み、マルチフィジックスでの網羅的かつ高速な最適化計算が実用的に使える段階に達しています。そこで、考えられる設計パターンについて、応力や熱といった複数の観点(マルチフィジックス)での3DCAE結果を最適化計算に掛けます。マルチフィジックスでの最適化により、トレードオフの解消も一度に図ることができます。
工程・設備設計でも同様に行います。概念・構想設計段階では、製品・機能設計部門から逐次共有される1DCAEやMODEの解析結果を受け、AI等を活用して最適な工法や設備の候補を導出します。たとえば、製品・機能設計部門からの部品サイズ等の情報を基に、使うべき設備をリストアップしたり、製造ラインの概略をデジタルツイン上に自動描画するとともに、必要な投資コストやリードタイムを見積もる。詳細設計段階では、製品・機能設計モデルをバーチャル空間上で連携し、工場・設備をデジタルツイン化 [2]します。工場のデジタルツインでは、組立・工程シミュレーションから、工場内の人の動線も含めたシミュレーションも可能となります。
条件モニタリング
生産段階では、品質バラツキを生む5M(Material、Machine、Man、Method、Measurement)条件のモニタリングにより、品質を制御/異常検出します。たとえば、切削時にマシニング加工に掛かる異常な応力や、溶接時の異常な電流から、AIにより品質異常をスクリーニングします。工場内の作業員をAIカメラでモニタリングすれば、各工程の作業状況や所要時間を計測でき、作業のヌケモレに対するアラームや、標準作業時間への指導が可能になります [4]。こうした5M条件のモニタリングは、比較的容易に行える場合があり、そして常時の計測が可能なため、低コストでの全数検査を可能にします。
なお、販売後つまりカスタマーサービス段階については、既に実践例も多くあります。有名な例としては、建機メーカーであるコマツのKOMTRAX [3]が挙げられます。KOMTRAXは、製品に装備したセンシング/通信装置により稼働状況を遠隔で把握できるシステムです。KOMTRAXにより適切な保守・メンテナンス時期の把握等ができるため、購入者・利用者だけでなくメーカー(コマツ)側からのプロアクティブな保守・メンテナンスサービスを実現しています。
パラレルな業務フローへの移行
全点モニタリング型の製品化プロセスは、業務フローの在り方を抜本的に変えることにも繋がります。前述のような全仕様に対する設計の品質モニタリングができれば、製品全体としてどこまで設計が進んでいるのか(言わばバーチャルな製品完成度)をいつでも把握できるようになります。さらに、トレサビを確立、全ての設計をバーチャル化して品質モニタリングできれば、機構/回路/ソフト/生産設計といった機能間や機能-生産要件間の整合性、つまり量産の実現性もいつでも判断できる可能性が生じます。従来なら、各設計が一段落した段階でデザインレビューを行い、設計進捗・成果の把握と次の開発ステップへの可否判断を行っていました。しかし、上記のような品質モニタリングができれば、審査ゲート(デザインレビュー)レスとなるため、全設計をパラレルで行えるようになります。特に従来では、設計出図後に生産側にて工程・設備設計というウォーターフロー型での運用が多いですが、この考え方を適用することでパラレル型への移行となり、設計出図と同時に生産準備完了を実現する可能性も高まります。これは真のコンカレントエンジニアリングと言えるでしょう。
進化するテクノロジーの活用
NQの全点モニタリング型のアプローチをバリューチェーン全体に適用するためには、最新テクノロジーの活用が欠かせません。設計段階では、CAD・CAEのフル活用や、マルチフィジックスでの最適化計算、スパコンでの計算高速化、デジタルツインでの工場バーチャル化が検討候補となります。生産段階では、センサー・通信装置を使った設備のIoT化、製品・作業者に対する検査機やAIカメラによるモニタリングが検討候補です。企画・開発初期段階では、AIによる要件抽出・整理、CADやPLMと連携するプラットホームによるトレサビ管理が挙げられます。
製造業においては製品開発プロセスにこれまで培った各社の技術・ノウハウが蓄積されているため、汎用的なソリューションを適用すれば済む話では無いと考えます。各社の独自性を尊重したプロセスと実現したい品質マネジメントレベルに応じたテクノロジーの活用が肝となります。
参考文献
[1] 従来型の品質マネジメントの限界
[2] https://business.nikkei.com/atcl/gen/19/00540/030800005/
[3] http://sanki.komatsu/komtrax/
[4] https://www.mediocritas.com/service/solution/
[1] 従来型の品質マネジメントの限界
[2] https://business.nikkei.com/atcl/gen/19/00540/030800005/
[3] http://sanki.komatsu/komtrax/
[4] https://www.mediocritas.com/service/solution/